Emulsion Storage Tank Leak
USING WATER-GLO® TO FIND THE SMALLEST, COSTLY LEAKS
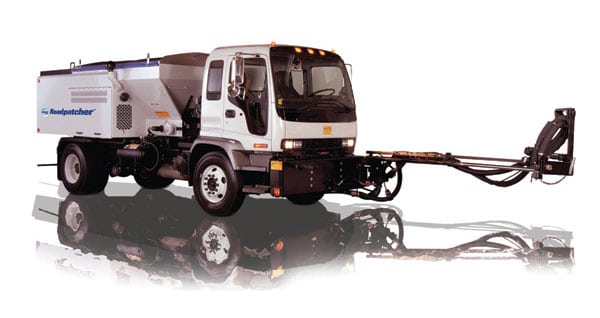
Spray patching is the process of dispensing emulsified asphalt over a damaged section of roadway.
Gravel is then added to the patching spray to reinforce the repair’s strength and durability. The boom outfitted on the truck is equipped with a high-speed air vent. When applied, the high-speed air quickly dries and solidifies the amalgamation – ensuring the repair is complete.
These specially designed spray patching trucks go along long tracts of roadway and quickly patch broken surfaces. But the trucks can contain a limited amount of emulsified asphalt. RCM’s storage tanks allow the emulsified asphalt to be towed separately, supplementing the spray truck’s main work. The storage tank is extremely useful on long and isolated tracts of roadway, and are an essential addition to any repair fleet.
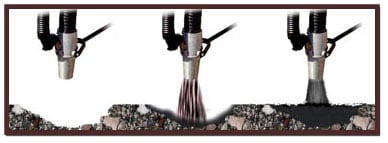

Rechargeable Industrial Leak Detection Lamp
A FLAW IN THE SYSTEM
Here’s The problem Frank Connelly’s team was facing: inside each of the emulsion storage tanks is a heat exchanger that maintains the operating temperature and allows the asphalt to be dispensed in a semi-liquid state. The storage tanks operate at temperatures up to 185 degrees Fahrenheit.
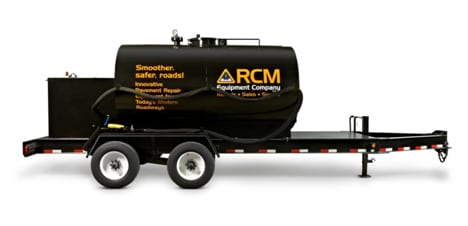
If the heat exchanger fails, the tank will overheat and the asphalt will become unusable. Because the storage tanks operate at high temperatures, the water glycol used in the heat exchanger evaporates before leaks can be detected.
TRIAL AND ERROR
The heat exchange coils within the storage tanks are constructed from schedule 40 piping and air-pressure tested to confirm a sealed system. When Frank’s team tried fixing the problem, they refitted the piping and pressure tested the system. But the pressure tests did not indicate any issues in the system.
After finding the air pressure tests results were normal, the team tried modifying the system to allow for extra capacity. The team modified the system with high-pressure rated valves. Frank’s team thought excess water glycol may have been forced out of system, during the high pressure and temperatures associated during prolonged operational use. Unfortunately, upgrading the system proved to be unsuccessful. The problem did not stem from the design to the tank – but a very small leak in the system that only became apparent during operational use.
SEARCHING FOR ANSWERS
Frank’s company tested the tank – but they could not locate the leak area. The team tried using a bubbling solution to help locate the leak. In addition to using the solution, Frank’s team tried isolating the heat exchange coils and testing them individually. Their efforts were unsuccessful.
RCM eventually resorted to using fluorescent leak detection dyes for automobiles, after having seen their efficacy in detecting leak areas in oil-based fluids. But the automotive dyes were unsuccessful because they were designed to be compatible with fluids of a lower viscosity than emulsified asphalt.
The RCM team then asked the manufacturers of the storage tanks to inspect the tank for flaws. But the storage tank was fine. And other companies who purchased the same storage tanks never had an issue. Frank and his team asked other companies in his line of work if they had ever experienced similar problems. But no one could give Frank a straight answer or even point him in the right direction.
When Frank and his team were unable to reach a solution themselves, they consulted online resources for answers. During their search, the team found the positive feedback and testimonials about the efficacy of Spectroline® dyes – capable of finding leaks better than any other dye manufacturer on the market, and endorsed by many OEMs such as Caterpillar, Komatsu, and John Deere Hitachi.
Frank’s team asked local contractors and professionals if the positive feedback was accurate. A local HVAC company Frank trusted confirmed the online testimonials: Spectroline® dyes are the highest quality dyes in the field for leak detection, outperforming all other dyes in the same price category.
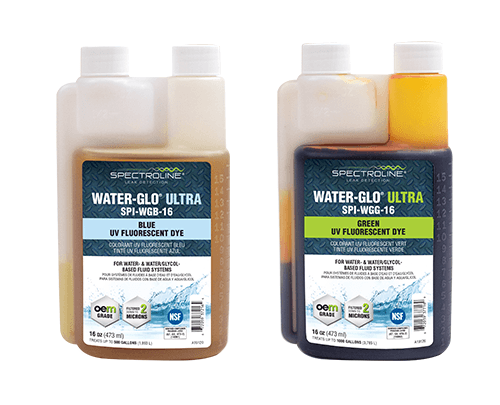
“WE PURCHASED ONE OF YOUR INDUSTRIAL (WATER-GLO®) LEAK DETECTION KITS…WE FOUND THE LEAK IN THE COIL WITHIN 5 MINUTES, OUR TEAM COULD NOT BELIEVE HOW WELL THE DYE SHOWED UP….IT IS NOW A STANDARD PROCEDURE TO ADD (WATER-GLO® GREEN) DYE TO THE HEATING SYSTEMS OF ALL OUR TANKS AND RUN THEM FOR 24 HOURS TO CHECK FOR LEAKS PRIOR TO DELIVERY.”
– FRANK CONNELLY, RCM EQUIPMENT COMPANY LLC.
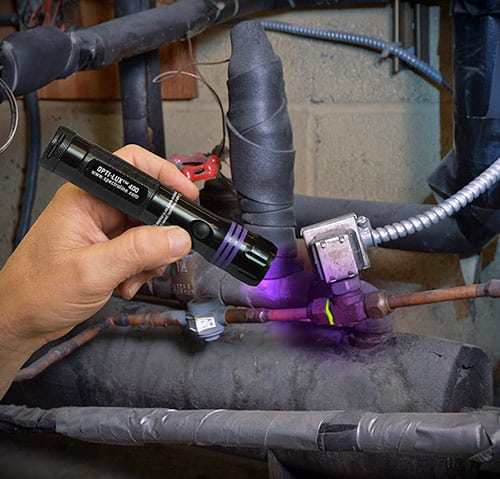
SOLVING THE PROBLEM, QUICKLY AND ACCURATELY
Within 10 minutes of adding the Spectroline® WATER-GLO® Green dye to the heat exchange system, the leak was clearly visible. Within 20 minutes of finding the leak, a weld was applied and the repair was confirmed. The leak was found to be within a 2-inch heating coil. Since the coils are custom welded to the RCM’s specifications, the room for error is always a possibility. And examining faults with the naked eye, during the welding process, isn’t enough to prove the weld was without fault. Out of the many leak detection methods used, only the specially designed WATER-GLO® series dyes for heat transfer fluid system applications found the leak.
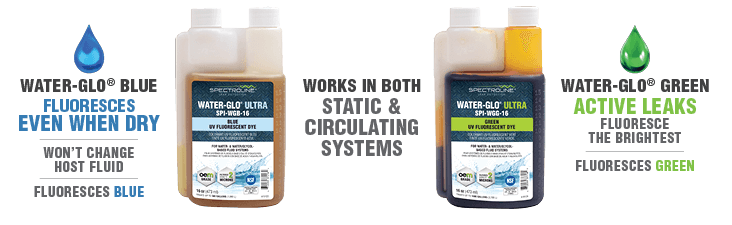
THE FUTURE OF RCM’S MANUFACTURING
In total, RCM incurred over $8,000 dollars in financial losses from wages, materials, and unsuccessful leak detection attempts. After discovering the issue could be resolved easily and without loss of time or energy, Frank is an advocate of Spectroline®’s line of WATER-GLO® dyes, specially designed for use in industrial applications. RCM now includes WATER-GLO® Green in their Quality Control Procedure by adding the fluorescent leak detection dye and running the system for 24 hours. Leaks in future tanks, based on RCM’s experience, will be easily identified and remedied in a short amount of time, with little loss in materials and labor.
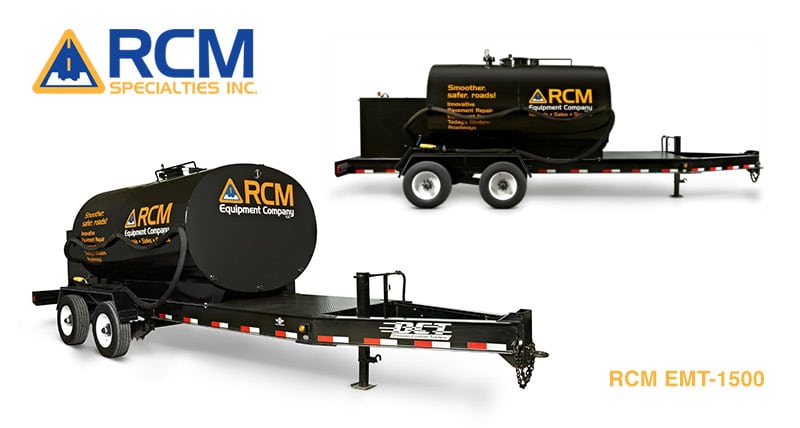
THE SPECTROLINE® ADVANTAGE
Part of the solution process, outside of the superior quality of the dye being applied, was the quality of the lamp being used to detect the dye’s fluorescence. Frank and his team used the OPTI-LUX™ 400, a compact but powerful ultraviolet leak detection flashlight. The flashlight is cordless and can be used in the tightest, hardest-to-reach spaces. The OPTI-LUX™ 400 has an inspection range of up to 25 feet (7.6 m) and is powered by a rechargeable lithium-ion battery, providing four hours of continuous inspection between charges.
The RCM team was especially amazed how easy the application process was. The team simply added the dye, ran the system for a limited amount of time, and the used the OPTI-LUX™ 400 flashlight to identify the leak area in question. Within minutes, the team detected the leak area. In future, thousands of dollars will be saved during the manufacturing and quality control process – guaranteeing RCM’s end-product is flawless and completely satisfactory.
Spectroline®’s patented fluorescent dyes provide superior leak detection and are trusted by major OEMs such as Caterpillar, Bobcat and Komatsu. Companies like Frank’s can hugely benefit from introducing Spectroline®’s expansive and targeted array of leak detection dyes to their manufacturing process. Whatever the situation, Spectroline® has come up the best and most reliable solution.
PROTECT YOUR EQUIPMENT. REDUCE DOWNTIME.
Join Our Mailing List and Stay Updated:
- Preventative Maintenance is key to saving time and money
Learn about the best maintenance practices and asset management tools. - Optimize your business and become an innovator
Ultraviolet fluorescent leak detection technology provides 100% accuracy.